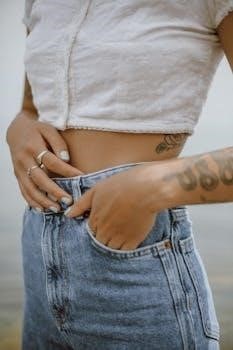
Pocket hole joinery offers a strong and efficient method for woodworking. This guide explains everything about pocket hole screws. From selecting the right size to understanding thread types, this guide will enhance your skills. It ensures strong and seamless connections in various projects.
Pocket hole joinery is a technique that utilizes angled holes drilled into one workpiece to join it to another with screws. This method creates a strong and concealed joint, ideal for various woodworking projects. It’s favored for its speed, simplicity, and the clean, screw-free appearance it offers on the visible surfaces of the finished piece.
The process involves using a specialized jig to drill a pocket hole at a specific angle, typically 15 degrees. After drilling, the piece is clamped to the second workpiece, and a self-tapping screw is driven through the pocket hole, drawing the two pieces together tightly. The screws are designed with a flat head that sits flush within the pocket hole, ensuring a secure and stable connection.
Pocket hole joinery is particularly useful in cabinet making, furniture construction, and frame assembly. Its ability to create strong joints quickly makes it a popular choice among both hobbyists and professional woodworkers. Furthermore, it allows for easy disassembly and adjustments if needed, adding to its versatility.
Choosing the right pocket hole screw is crucial to the success of this joint. Factors like wood thickness, screw length, and thread type must be carefully considered to ensure a robust and lasting bond. This guide will help you navigate these choices for optimal results.
Understanding Pocket Hole Screws
Pocket hole screws are specially designed fasteners used in pocket hole joinery to create strong, reliable joints. These screws differ from standard wood screws in several key aspects, making them uniquely suited for this specific application. Understanding these differences is crucial for selecting the right screw for your project.
One of the primary features of pocket hole screws is their self-tapping ability. This eliminates the need for pre-drilling pilot holes, saving time and ensuring accurate screw placement. The screws also feature a flat head designed to sit flush within the pocket hole, preventing the screw from protruding and interfering with the joint’s integrity.
The thread pattern on pocket hole screws is another important consideration. They are available in both coarse and fine threads. Coarse-threaded screws are best for softwoods and materials like plywood and particleboard, as they provide a stronger grip. Fine-threaded screws are better suited for hardwoods, as they are less likely to strip the wood fibers.
Screw length is also critical. The length of the screw should be appropriate for the thickness of the wood being joined. Using too short a screw will result in a weak joint, while using too long a screw can cause it to protrude through the material.
Choosing the Right Screw Size
Selecting the correct screw size is crucial for strong pocket hole joints. Consider wood thickness and screw length to prevent weak joints or protrusions. Choose coarse or fine threads based on whether you are using hardwood or softwood.
Wood Thickness and Screw Length
Matching screw length to wood thickness is paramount in pocket hole joinery. If screws are too short, the joint’s strength will be compromised, leading to potential failure under stress. Conversely, screws that are too long may protrude through the material, creating an unsightly finish and potentially interfering with the project’s functionality.
A general rule of thumb is to select a screw length that allows for adequate thread engagement in the receiving workpiece without penetrating the opposite surface. Consult screw selection charts, which correlate wood thickness with appropriate screw lengths, ensuring optimal joint integrity. The precise metric scale is really important and you should use it.
For thinner materials, shorter screws are necessary to prevent breakthrough, while thicker materials require longer screws for secure fastening. Also, always measure precisely the screw length to prevent damage to the material.
Always test the joint with scrap material to verify screw length before committing to the final assembly. This simple step can save time, materials, and frustration, ensuring a professional-quality result.
Consider the density of wood when selecting the length.
Coarse vs. Fine Thread Screws
The choice between coarse and fine thread screws is crucial for successful pocket hole joinery, primarily determined by the wood’s density. Coarse thread screws, with their deeper, more widely spaced threads, excel in softer materials like plywood, MDF, and softwoods. These threads bite aggressively into the wood fibers, providing a strong, reliable hold that resists pull-out.
Fine thread screws, characterized by their shallow, closely spaced threads, are ideal for hardwoods such as maple, oak, and cherry. The finer threads prevent stripping in these denser materials, ensuring a secure connection without damaging the wood.
Selecting the incorrect thread type can lead to joint failure. Using fine thread screws in softwoods may result in inadequate grip, while coarse thread screws in hardwoods can strip the threads, weakening the joint.
Always consider the wood species when choosing screws. Also, always test the screw to check the quality of the screw. Always use the right screws for the best result.
Screw Head Types
Selecting the right screw head is vital for pocket hole joinery, impacting both function and aesthetics. Two common types are pan head and washer head screws. Each is designed for specific applications, ensuring optimal performance and a clean finish.
Pan Head Screws
Pan head screws are distinguished by their slightly rounded top surface and a flat bearing surface. This design allows the screw to sit flush with the material surface, providing a neat and professional appearance. The pan head’s shape distributes pressure evenly, reducing the likelihood of the screw head sinking into the wood, particularly in softer materials.
These screws are versatile and suitable for a wide range of pocket hole applications. They are commonly used in general woodworking projects where a flush or near-flush finish is desired. The design ensures that the screw head doesn’t interfere with mating surfaces or hardware. The broad bearing surface helps to prevent pull-through, making them a reliable choice for various wood types and thicknesses.
When selecting pan head screws, it’s crucial to consider the material’s density. Softer woods may require a finer thread to ensure a secure hold, while harder woods may benefit from a coarser thread. The screw length should also be appropriate for the wood thickness to provide adequate clamping force without protruding through the joint. With the correct selection, pan head screws offer both functionality and aesthetic appeal in pocket hole joinery.
Washer Head Screws
Washer head screws are characterized by a flat head with an integrated washer. This washer increases the bearing surface of the screw, providing enhanced clamping force and preventing the screw from pulling through the material. The wider head distributes pressure more evenly, making these screws ideal for softer woods or applications where high holding power is required.
The design of washer head screws makes them particularly useful in situations where the joint is subjected to significant stress or vibration. The increased bearing surface minimizes the risk of the screw head sinking into the wood, ensuring a secure and stable connection. These screws are commonly used in furniture construction, cabinet making, and other projects where durability and strength are essential.
When selecting washer head screws, it is crucial to choose the appropriate length and thread type for the specific application. Longer screws are necessary for thicker materials, while the thread type should be matched to the density of the wood. Coarse threads are generally preferred for softwoods, while fine threads are better suited for hardwoods. Proper selection ensures optimal holding power and a long-lasting, reliable joint.
Setting Up Your Pocket Hole Jig
Proper setup is essential for accurate pocket holes. Adjust the jig according to the wood thickness. This ensures the correct angle and depth for the screw. A precise setup yields strong joints.
Adjusting the Drill Guide
Adjusting the drill guide on your pocket hole jig is a critical step in ensuring successful and accurate joinery. The drill guide’s position dictates the angle and depth of the pocket hole, directly impacting the strength and appearance of the final joint. Begin by identifying the thickness of the wood you’ll be working with. Most pocket hole jigs come with a clear, marked scale, often metric, to assist in this process.
Loosen the thumb screw or adjustment mechanism that secures the drill guide. This will allow you to slide it up or down to the appropriate setting. Align the indicator on the drill guide with the corresponding wood thickness on the scale. Ensure the setting is precise, as even slight deviations can affect the screw’s trajectory and holding power. Once aligned, firmly tighten the thumb screw to lock the drill guide in place.
Test the setup on a piece of scrap wood of the same thickness. Drill a pocket hole and drive a screw to check if the screw sits flush with the surface and the joint is tight. If adjustments are needed, repeat the process until the desired result is achieved. Accurate drill guide adjustment is vital for consistent and reliable pocket hole joinery.
Driving Pocket Hole Screws
Driving pocket hole screws correctly is crucial for creating strong and reliable joints. After drilling the pocket hole and clamping the pieces together, select the appropriate screw for the wood thickness and type. Ensure you’re using the correct thread (coarse for softwoods, fine for hardwoods) and length. Position the screw tip into the pocket hole, aligning it with the pilot hole in the adjoining piece.
Use a variable-speed drill or impact driver with a square-drive bit to drive the screw. Start slowly to prevent the screw from stripping or wandering. Apply steady, even pressure to keep the screw aligned. Drive the screw until it’s snug, but avoid over-tightening, which can split the wood or strip the screw head. The screw head should sit flush with the bottom of the pocket hole.
For larger projects, consider using a self-adjusting face frame clamp to hold the pieces together while driving the screws. This ensures a tight, even joint. After driving all the screws, inspect the joint for any gaps or misalignments. If necessary, loosen the screws slightly and adjust the pieces before re-tightening. With proper technique and attention to detail, you can achieve strong, seamless pocket hole joints every time.